DISTILLING
Distillation is one of the fundamental processes used in crude oil refineries to separate crude oil into different fractions based on their boiling points. The process involves heating crude oil in a distillation column, where the various components of the crude oil are vaporized and then condensed into separate fractions.
The distillation process begins with the heating of crude oil in a furnace or a preheat train to temperatures typically ranging from 350°C to 400°C. The heated crude oil is then introduced into the bottom of a distillation column, which is a tall, vertical vessel that is divided into multiple trays or stages. The number of trays or stages depends on the type of crude oil and the desired product specifications.
As the heated crude oil rises up the distillation column, it vaporizes and enters the various trays or stages at different heights. Each tray or stage has a slightly lower temperature than the one below it, which causes the vaporized components to condense and collect on the tray or stage. The components with the lowest boiling points, such as light hydrocarbons, rise to the top of the column and are collected as overhead vapor. The heavier components, such as diesel fuel and lubricating oil, condense and collect on the lower trays or stages.
The trays or stages in the distillation column are equipped with valves that can be adjusted to control the temperature and pressure of the vapor and liquid streams. This allows operators to optimize the distillation process for specific product specifications and to minimize the amount of energy required to operate the column.
After the distillation process is complete, the various fractions are collected and sent to other processing units for further treatment and refining. For example, the naphtha fraction may be sent to a catalytic reforming unit to produce high-octane gasoline, while the diesel fraction may be sent to a hydrotreating unit to remove sulfur and other impurities.
In summary, the distillation process in a crude oil refinery is a critical step in the refining process that separates crude oil into various fractions based on their boiling points. The process involves heating crude oil and introducing it into a distillation column, where it is separated into different fractions based on their condensation temperatures. The various fractions are then sent to other processing units for further treatment and refining. The distillation process is essential for producing a range of petroleum products that are used in transportation, industry, and everyday life
CRACKING
Cracking is a process used in crude oil refining to break down larger, heavier hydrocarbon molecules into smaller, lighter ones. This process is essential for the production of high-value products such as gasoline, diesel fuel, and jet fuel, which require lighter hydrocarbons. Cracking can be achieved through various methods, including thermal cracking, catalytic cracking, and hydrocracking.
Thermal cracking is the oldest and simplest method of cracking, which involves the heating of crude oil to high temperatures, typically in the range of 450-500°C, and then rapidly cooling it. This causes the heavier hydrocarbons to break down into lighter ones, which can then be separated into different fractions. The primary disadvantage of thermal cracking is that it is inefficient and produces a large amount of coke, a solid carbon residue that can damage equipment and reduce product yields.
Catalytic cracking, on the other hand, is a more efficient method of cracking that uses a catalyst to accelerate the reaction rate and reduce coke formation. The process involves the use of a zeolite catalyst, which is a type of porous material that can selectively break down larger hydrocarbons. The catalyst is typically mixed with the crude oil before it enters the reactor, where it breaks down the larger molecules into smaller ones. The lighter fractions produced in the process are then separated and sent to other processing units for further treatment.
Hydrocracking is a more advanced form of catalytic cracking that combines the use of a catalyst with hydrogen gas. The process involves the use of a high-pressure reactor, which is filled with a catalyst and hydrogen gas. The crude oil is then injected into the reactor, where it is cracked into smaller molecules under high temperature and pressure. The hydrogen gas reacts with the hydrocarbons to remove sulfur and other impurities, resulting in a cleaner product. The lighter fractions produced in the process can be further processed into high-value products such as gasoline and diesel fuel.
In summary, cracking is a process used in crude oil refining to break down larger, heavier hydrocarbon molecules into smaller, lighter ones. This process is essential for the production of high-value products such as gasoline, diesel fuel, and jet fuel, which require lighter hydrocarbons. Cracking can be achieved through various methods, including thermal cracking, catalytic cracking, and hydrocracking. Each method has its advantages and disadvantages, and the choice of method depends on the specific product requirements and the type of crude oil being processed
REFORMING
Reforming is a process used in crude oil refining to convert low-octane naphtha into high-octane gasoline. The process involves the use of a catalyst to rearrange the molecular structure of the naphtha, which increases its octane rating and improves its performance in engines. Reforming is an essential process in the production of high-quality gasoline, which is a critical component of transportation fuels.
The reforming process is typically carried out using a platinum or platinum-rhenium catalyst in a fixed-bed reactor. The naphtha feedstock is preheated and then mixed with hydrogen gas before entering the reactor. The mixture then flows through the catalyst bed, where it is heated to high temperatures and high pressure, typically in the range of 500-600°C and 50-60 atmospheres.
The catalyst promotes a series of chemical reactions, including dehydrogenation, isomerization, and cyclization, that break down the larger hydrocarbons in the naphtha and rearrange them into smaller, more branched molecules. The result is a product with a higher octane rating and improved performance in engines.
After the reforming process is complete, the product is sent to a fractionation unit, where it is separated into various fractions based on their boiling points. The high-octane gasoline is then blended with other components, such as ethanol and other additives, to meet specific product specifications.
Reforming is a complex process that requires careful control of temperature, pressure, and catalyst activity to achieve optimal product yields and performance. The process is typically carried out in multiple stages, with the product from each stage being sent to a fractionation unit before being combined with other components. The choice of catalyst and operating conditions depends on the specific feedstock and product requirements.
In summary, reforming is a process used in crude oil refining to convert low-octane naphtha into high-octane gasoline. The process involves the use of a catalyst to rearrange the molecular structure of the naphtha, which increases its octane rating and improves its performance in engines. The reforming process is essential in the production of high-quality gasoline, which is a critical component of transportation fuels. The process is complex and requires careful control of temperature, pressure, and catalyst activity to achieve optimal product yields and performance.
TREATING
Treating is a process used in crude oil refining to remove impurities from the crude oil and other feedstocks. The process is essential to ensure that the final products meet the required specifications and are safe for use. The treating process involves several steps, including desalting, sweetening, and sulfur removal.
Desalting is the first step in the treating process and involves the removal of salts and other impurities, such as water and sediments, from the crude oil. The process is typically carried out using electrostatic or mechanical methods, such as settling tanks, centrifuges, or hydrocyclones. In electrostatic desalting, an electrical charge is applied to the crude oil as it passes through a series of electrodes, causing the impurities to separate and settle at the bottom of the tank. Mechanical methods involve the use of centrifugal force to separate the impurities from the crude oil.
Sweetening is the next step in the treating process and involves the removal of sulfur and other acidic impurities from the crude oil. The process is typically carried out using a process called hydrotreating, which involves the use of hydrogen gas and a catalyst to remove the sulfur and other impurities. The process is typically carried out in a high-pressure reactor, where the crude oil is mixed with hydrogen gas and the catalyst. The mixture is then heated to high temperatures and pressures, typically in the range of 350-400°C and 50-60 atmospheres. The catalyst promotes a series of chemical reactions that convert the sulfur compounds into hydrogen sulfide, which is then removed from the mixture.
Sulfur removal is the final step in the treating process and involves the removal of any remaining sulfur compounds from the product streams. The process is typically carried out using a process called sulfur recovery, which involves the use of a series of steps, including Claus process and tail gas treatment unit. The Claus process involves the use of high temperature and pressure to convert the hydrogen sulfide gas into sulfur dioxide gas, which is then reacted with oxygen to form elemental sulfur. The tail gas treatment unit recovers the remaining sulfur compounds from the tail gas, which is then returned to the Claus process.
Treating is a critical process in crude oil refining that ensures the final products meet the required specifications and are safe for use. The process involves several steps, including desalting, sweetening, and sulfur removal, which are typically carried out using a combination of mechanical, chemical, and catalytic methods. The choice of method and operating conditions depends on the specific feedstock and product requirement
BLENDING
Blending is a process used in crude oil refining to produce final products, such as gasoline, diesel fuel, and other petroleum products, with the desired specifications. The process involves combining different components, such as crude oil, intermediate products, and additives, to produce a final product with the desired properties, such as octane rating, cetane number, and viscosity.
The blending process typically involves several steps, including component selection, mixing, and quality control. Component selection involves choosing the appropriate components, such as different grades of crude oil, intermediate products, and additives, to achieve the desired product specifications. The selection of components is based on factors such as product demand, availability, and cost.
Once the components have been selected, they are mixed in a blending unit, which typically consists of a series of tanks and pumps. The components are combined in specific proportions to produce the desired product specifications. The mixing process is typically controlled using computer systems that monitor the flow rates and tank levels to ensure that the correct proportions are maintained.
Quality control is an essential part of the blending process and involves testing the final product to ensure that it meets the required specifications. Quality control tests typically include measurements of properties such as density, viscosity, and octane or cetane number. The tests are carried out at various stages of the blending process, including before and after blending, to ensure that the final product meets the required specifications.
Blending is a complex process that requires careful control of component selection, mixing, and quality control to ensure that the final product meets the required specifications. The process is typically carried out using advanced computer systems that monitor and control the flow rates and tank levels to ensure that the correct proportions are maintained. The choice of components and the blending process parameters depend on the specific product requirements and market demand.
In summary, blending is a process used in crude oil refining to produce final products with the desired specifications. The process involves selecting appropriate components, mixing them in specific proportions, and carrying out quality control tests to ensure that the final product meets the required specifications. The process is complex and requires careful control of component selection, mixing, and quality control to ensure that the final product meets the desired properties.
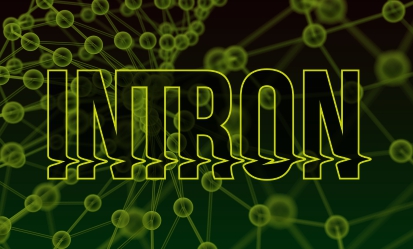
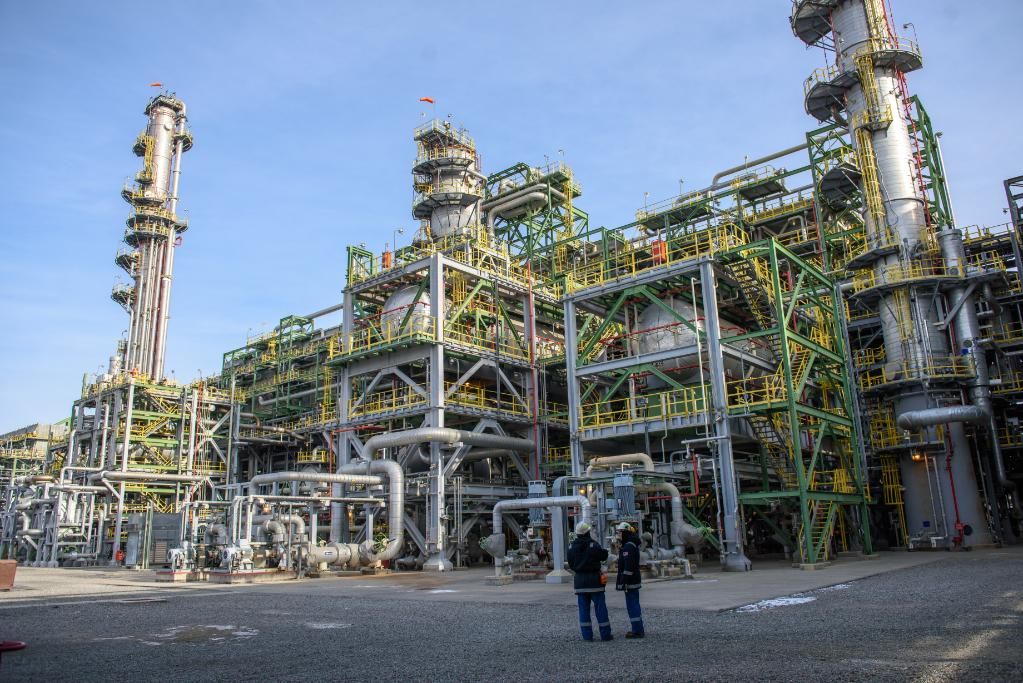
Our core solutions for refinery processes
- INTRON® antiCor
- INTRON® Cure N
- INTRON® antiTar
- INTRON® antiOx
- INTRON® deFoamer
- INTRON® dSol
- INTRON® dFlow
- INTRON® Wax
- INTRON® cTane
- INTRON® dLube
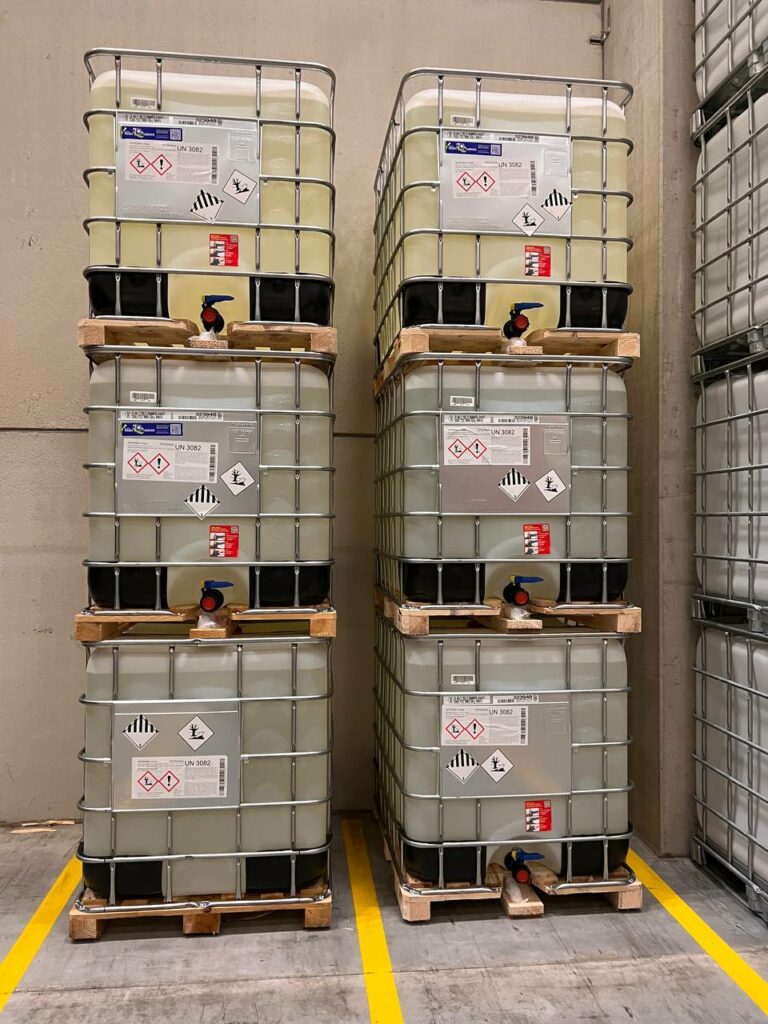
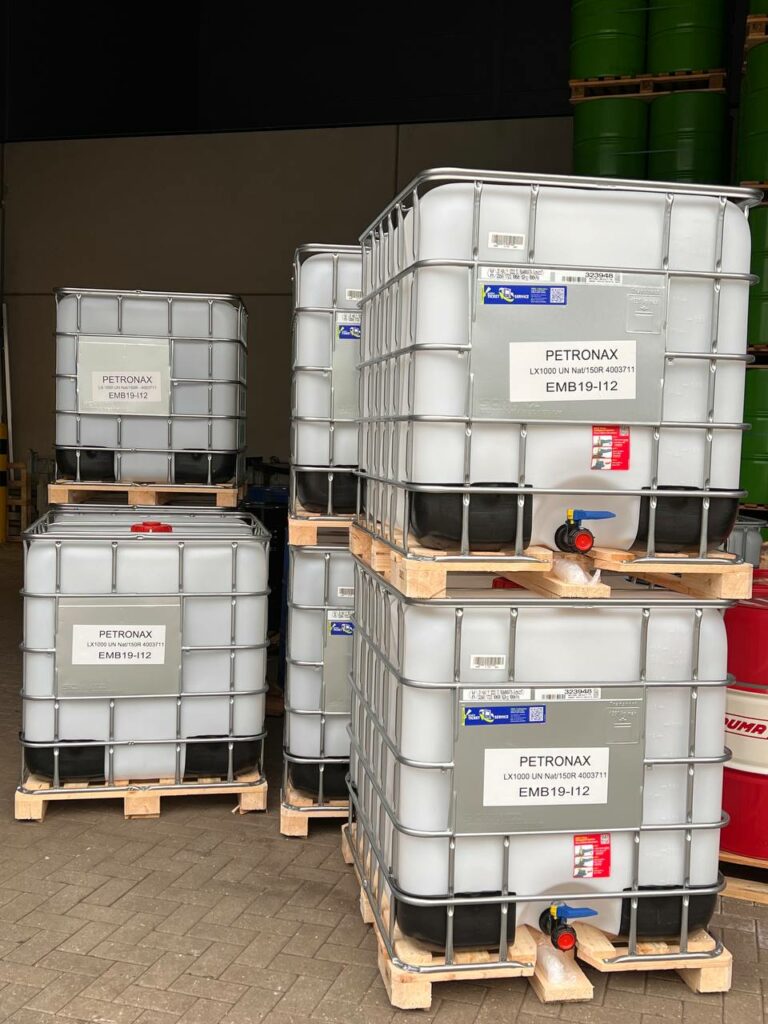
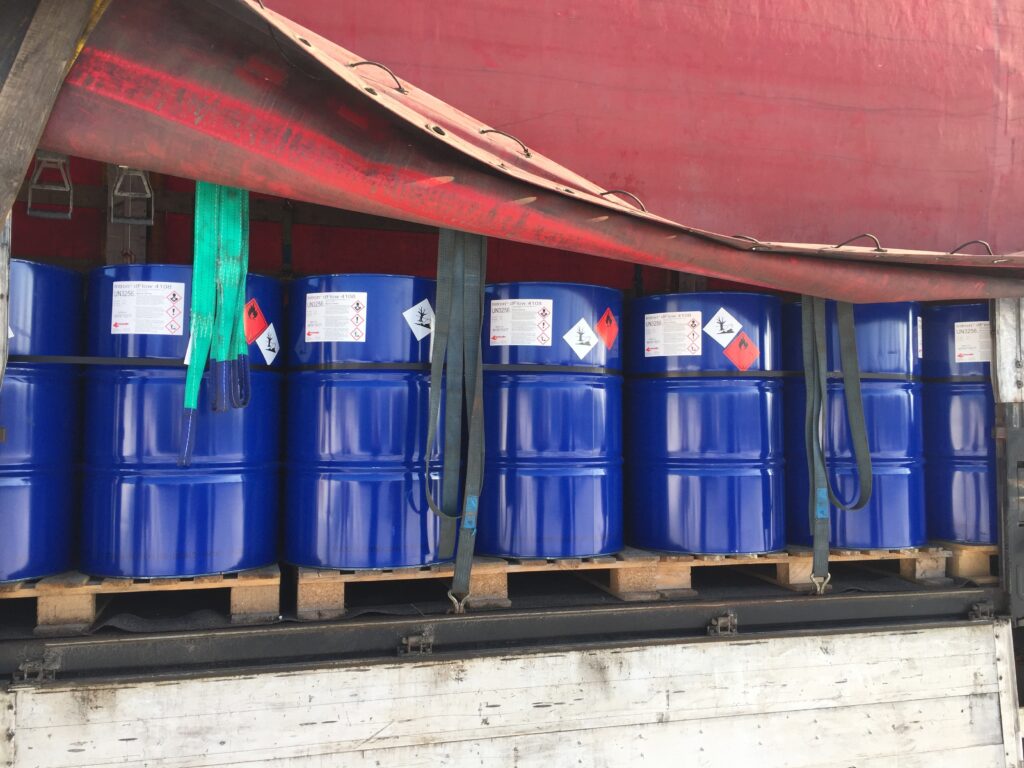
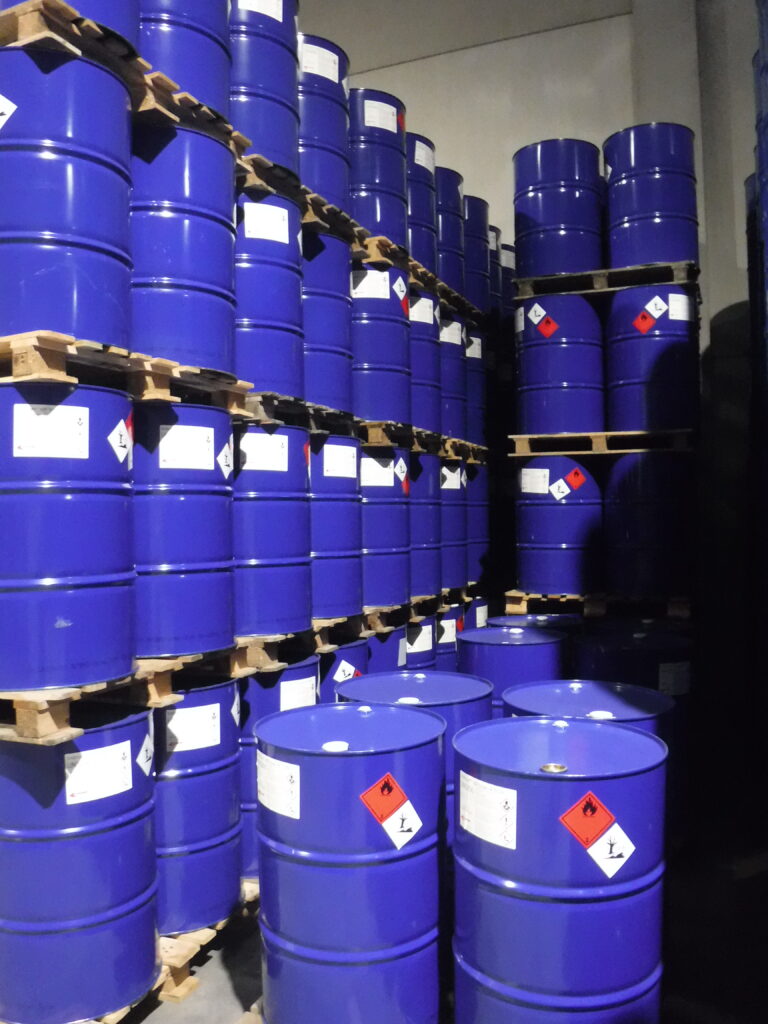
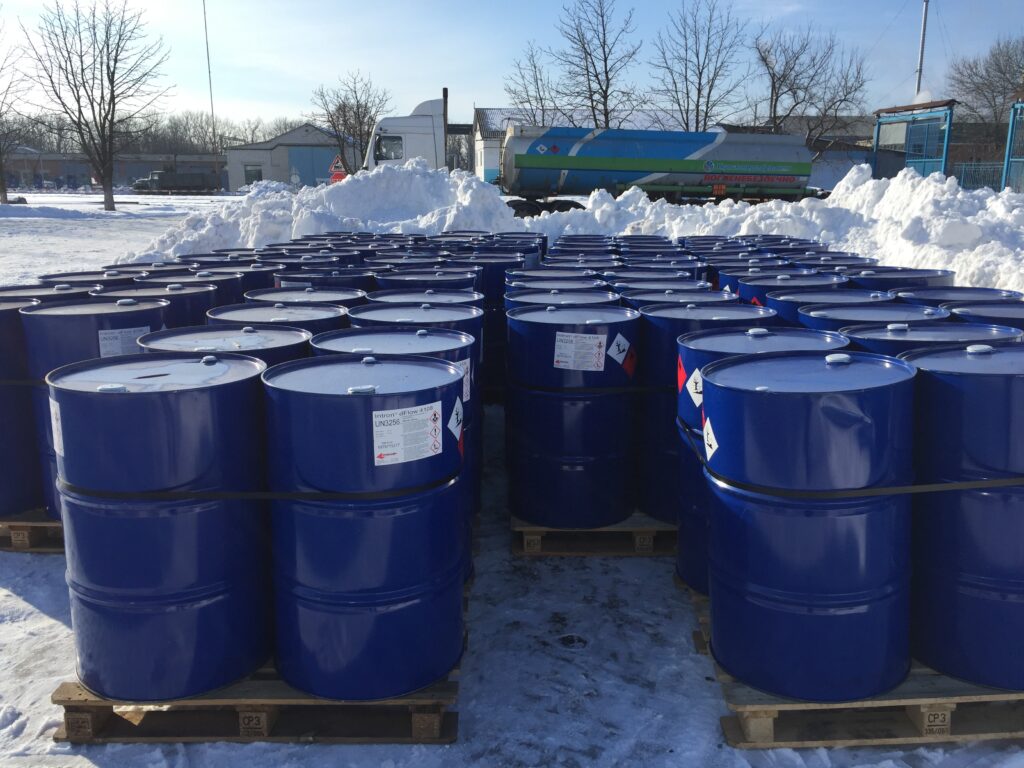